
In this application, a single composite monoleaf spring is mounted transverse to the vehicle's frame beneath a rear suspension cross member and supports at each of its outboard ends the lower end of a rear wheel spindle. One particular application of this spring is in the independent rear suspension system of GM's W-body automobile line produced between 19. GM has employed such springs in the suspension systems of many of their automobile lines.
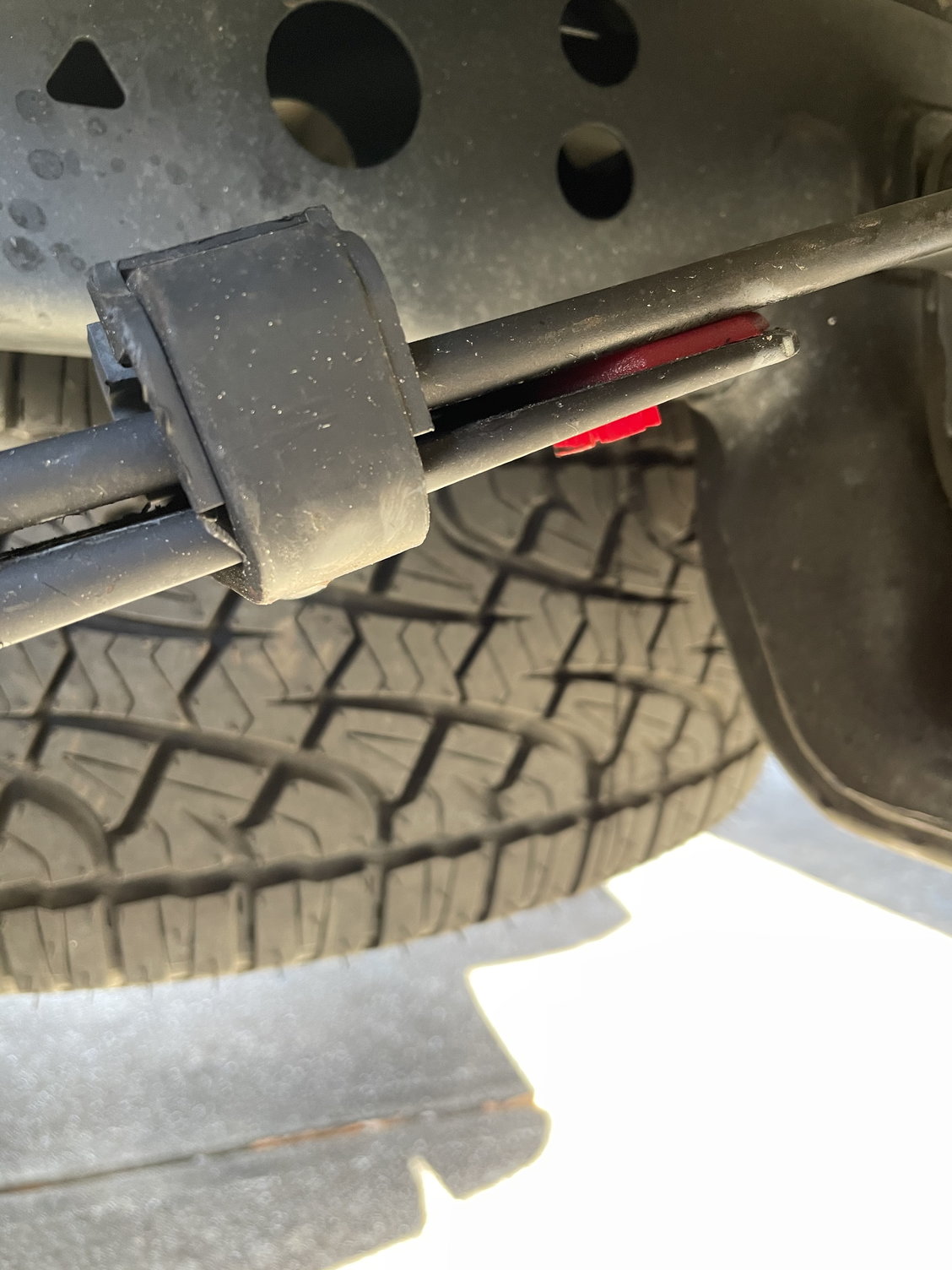
This monoleaf spring design is made from a composite glass fiber/epoxy resin which is formed and cured to provide sufficient strength and flexibility to suspend a motor vehicle. One of the more popular composite leaf spring designs is manufactured by the Inland Division of General Motors Corporation (GM). Down time due to spring problems is virtually eliminated with composite leaf springs. Additionally, laboratory fatigue tests have shown that composite leaf springs are up to five times more durable than conventional multi-leaf steel springs.
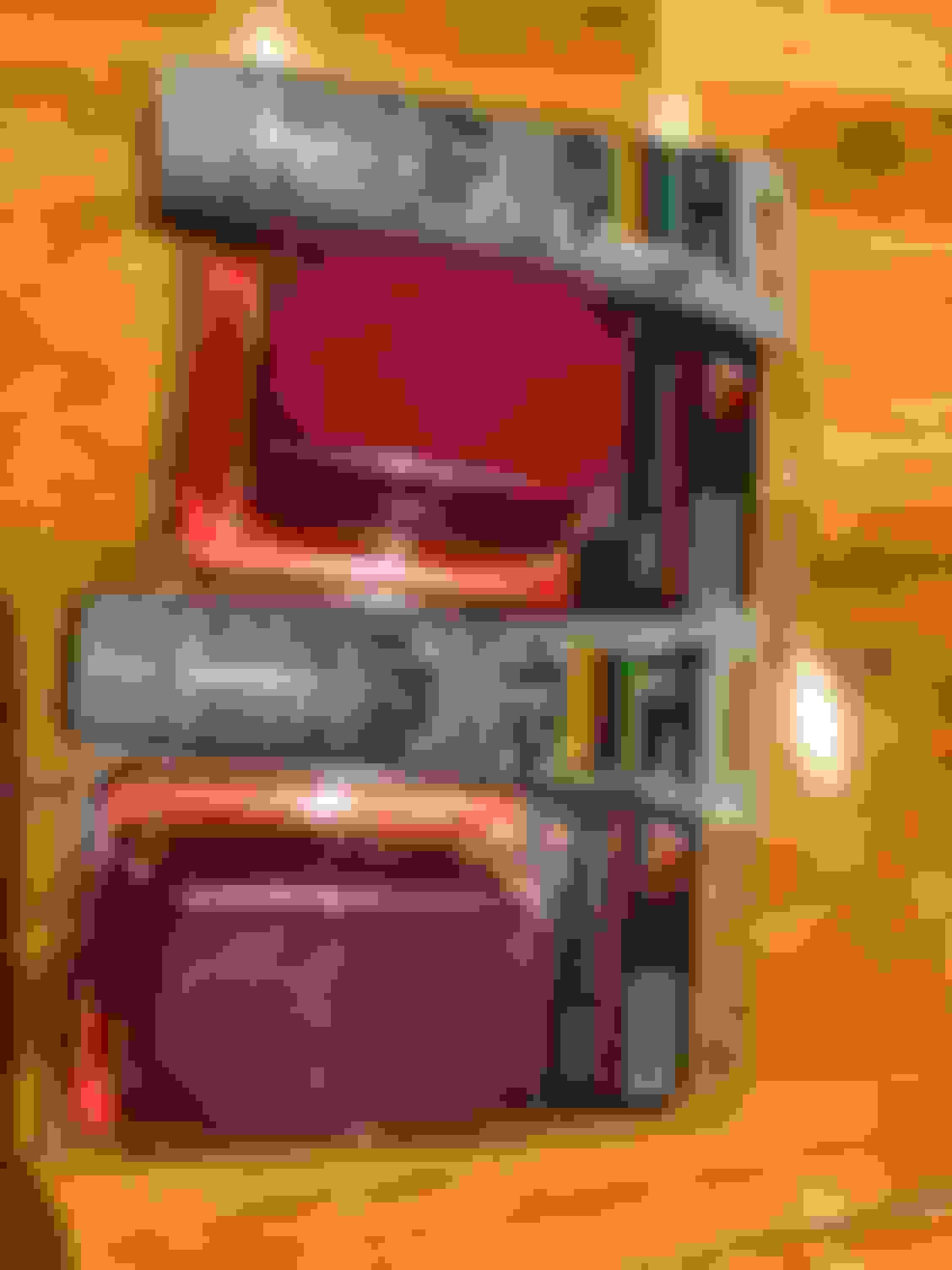
In most applications, at least a 60% weight reduction is realized. BACKGROUND OF THE INVENTIONĬomposite leaf springs offer both weight and space savings over conventional coil and metal leaf spring designs used in motor vehicle suspension systems although, the most significant advantage of the composite spring is in the reduction of weight. The present invention relates to isolator pads for motor vehicle leaf springs, and more particularly, to a plastic isolator pad for supporting the outboard ends of a transverse mounted composite mono-leaf spring.
